Quality Control in Manufacturing: Exploring the Path to Improved Processes with ISO 9001 Certification
In the ever-competitive world of manufacturing, ensuring consistent quality is paramount. Customers demand products that meet their expectations, and manufacturers strive to deliver excellence. This is where ISO 9001 comes in. As an ISO standards expert, I invite you on an exploratory journey to understand how ISO 9001 certification can revolutionize your quality control processes.
What is ISO 9001? A Framework for Quality Excellence
ISO 9001 is the world’s most widely recognized standard for quality management systems (QMS). It outlines a set of principles and requirements that organizations can follow to establish a robust quality management framework. This framework is not prescriptive; it provides a flexible structure that manufacturers can adapt to their specific needs.
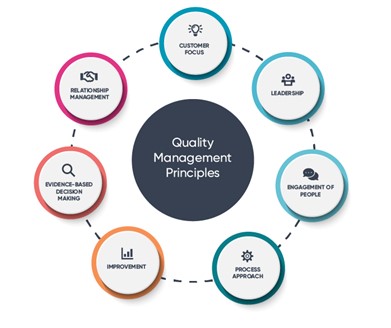
Why Explore ISO 9001 for Your Manufacturing Operations?
Here’s why exploring ISO 9001 certification can be a transformative step for your manufacturing company:
- Enhanced Customer Satisfaction: By focusing on meeting and exceeding customer requirements, ISO 9001 helps you build trust and loyalty with your customers.
- Improved Process Efficiency: The standard promotes a focus on continuous improvement, leading to streamlined processes, reduced waste, and optimized production times..
- Reduced Costs: Minimizing errors and defects translates to cost savings on rework, scrap materials, and warranty claims. [Infographic: Show a line graph with "Manufacturing Costs" on the Y-axis and "Time" on the X-axis. Plot two lines: one for "Without ISO 9001" showing a gradual increase in costs over time, and one for "With ISO 9001" showing a steady decrease or flatline in costs.
- Stronger Risk Management: ISO 9001 emphasizes proactive risk identification and mitigation, minimizing the potential for disruptions and ensuring operational stability.
- Competitive Advantage: Certification demonstrates your commitment to quality, potentially opening doors to new markets and partnerships.
Exploring the Core Principles of ISO 9001
The standard is built upon a foundation of eight core principles, all of which contribute to a robust quality management system:
- Customer Focus: Understanding and meeting customer needs is paramount.
- Leadership: Management commitment drives quality initiatives.
- Engagement of People: Empowering employees is crucial for success.
- Context of the Organization: Understanding your operating environment is vital
- Continuous Improvement: A relentless pursuit of better.
- Fact-Based Decision Making: Data drives effective decisions.
- Relationship Management: Strong supplier relationships are essential.
- Improvement: Continually improve all processes.
Exploring the Path to Achieving ISO 9001 Certification
Obtaining ISO 9001 certification requires a dedicated effort. Here’s a simplified exploration of the process:
- Gap Analysis: Assess your current quality management system against the ISO 9001 requirements.
- Develop a QMS: Develop and document your quality management system based on ISO 9001.
- Implementation: Implement the QMS throughout your organization.
- Internal Audit: Conduct an internal audit to verify your QMS effectiveness.
- Certification Audit: Undergo a formal audit by an accredited certification body.
The Exploration Continues: Beyond Certification
Achieving ISO 9001 certification is just the beginning. The true value lies in the ongoing application of these principles to continuously improve your quality control processes. By embracing a culture of continuous improvement, you ensure that your manufacturing operations remain agile and responsive in the ever-evolving marketplace.
Embrace the Exploration: Invest in Quality
Exploring ISO 9001 certification is an investment in the future of your manufacturing company. By implementing a robust quality management system, you create a foundation for consistent excellence, customer satisfaction, and long-term success. As an ISO standards expert, I encourage you to embark on this exploratory journey and unlock the full potential of your quality control processes.